Antes de que un coche llegue al mercado, los fabricantes deben superar una serie de pruebas. Entre otras muchas, las más llamativas quizá sean las de impacto. Tratan de garantizar un determinado nivel de seguridad tanto para los ocupantes del propio vehículo como para terceros (por ejemplo, un peatón o un ciclista).
Centro de pruebas Polygon
Škoda nos ha invitado a conocer el lugar donde realiza esas y otras pruebas de seguridad (no es habitual que un fabricante abra las puertas de estas instalaciones a la prensa). Recibe el nombre de Polygon y está situado en el municipio de Úhelnice, cerca de Mladá Boleslav (República Checa). Este centro pertenece a Škoda desde 2011, aunque también lo utiliza la TÜV SÜD de ese país.
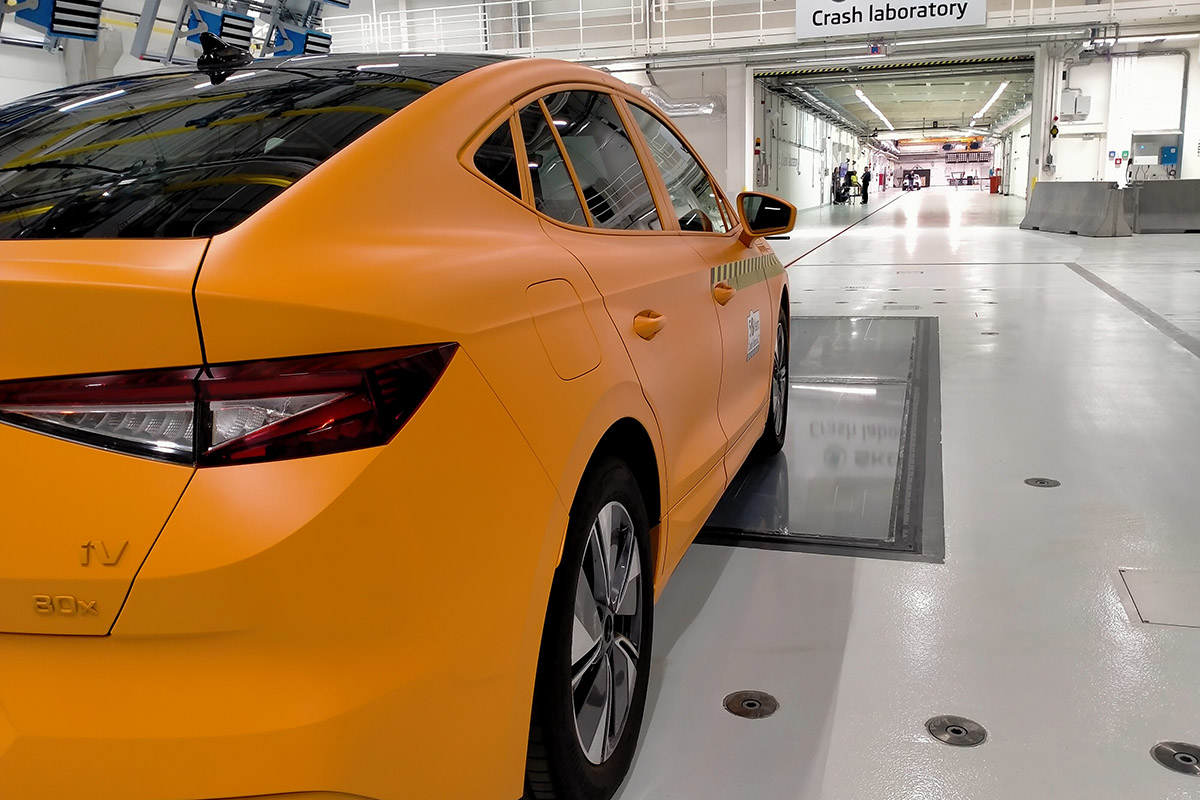
El edificio está en mitad de una zona arbolada y apartada a unos cientos de metros de Úhelnice. Las proporciones del edificio son curiosas. El cuerpo principal es una construcción alargada con una cavidad interior de unos 180 metros de longitud, lo cual tiene su explicación como veremos más adelante. Por dentro, el Polygon se parece más a un laboratorio gigante que a cualquier otra cosa. Las paredes y los techos son de un tono gris claro y un blanco casi níveo, el techo está plagado de focos potentes que crean una iluminación que abraza cada rincón reduciendo al máximo las sombras. Hay más puntos de luz, distribuidos en parrillas, que se utilizan para que las cámaras de alta velocidad puedan captar todos los detalles de las distintas pruebas.
Laboratorio de simulaciones
Esa sensación de laboratorio se ve reforzada por el instrumental que se ve alrededor: maniquíes de ensayo (conductores, peatones y ciclistas), esferas que simulan cabezas, piezas alargadas recubiertas de espuma a modo de piernas, coches desprovistos de guarnecidos y con los airbags desplegados, carretillas de impacto, coches inflables, sillas infantiles, guardarraíles, instrumental de diverso tipo, etc.
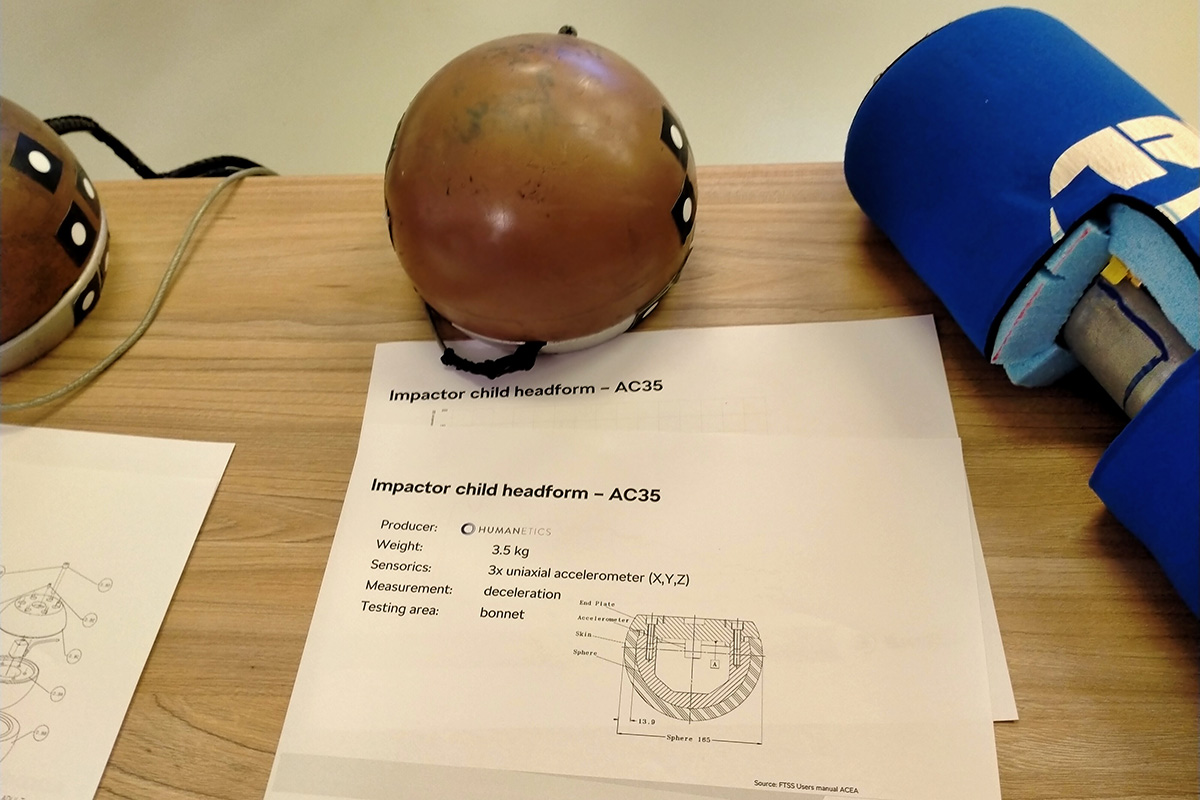
Gran parte de los 180 metros del edificio principal se utilizan para acelerar el vehículo, enganchado a un cable de acero encarrilado por debajo del piso, que impactará contra otro coche u otro obstáculo. Que sea tan largo es importante, según Škoda, para que la aceleración sea suave y los dummies no se muevan antes del impacto. Bajo el suelo de esa nave principal hay una planta subterránea donde está la maquinaria eléctrica que, a modo de tirachinas gigante, puede acelerar un vehículo hasta 120 km/h, o dos en dirección contraria hasta 65 kilómetros por hora (siempre que pesen menos de 3,5 toneladas en total) en el caso de impactos frontales.
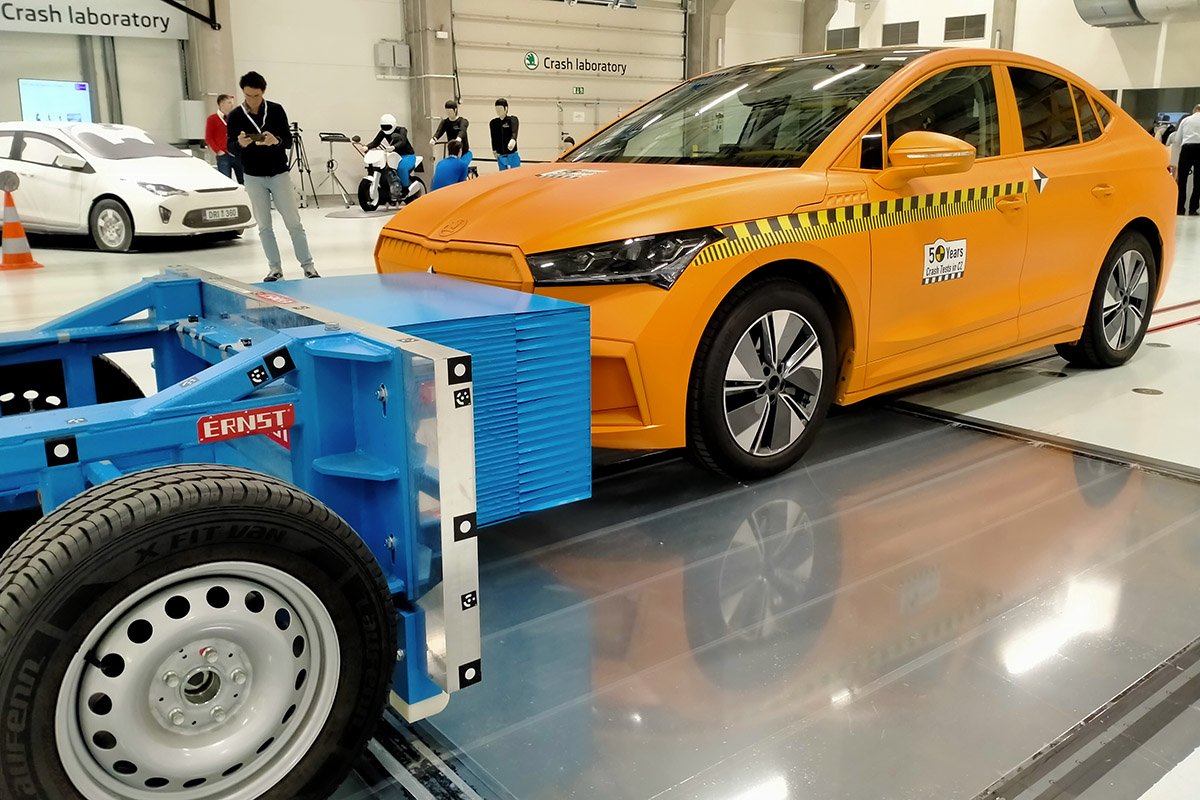
Primeras pruebas de impacto: carretilla-cohete
Pero no siempre fue así. Las primeras pruebas de impacto oficiales de Škoda de las que hay registros fueron en 1972 (la marca dice que las primeras podrían haber tenido lugar ya en 1968). Škoda quería vender su modelo 100L en Europa occidental, donde era obligatorio cumplir con una normativa de seguridad (no era necesario en Checoslovaquia). Las pruebas se llevaron a cabo en una zona de la pista de aterrizaje del aeropuerto Václav Havel. ¿Y cómo se aceleró el coche hasta los 50 kilómetros por hora a los que se quería impactar ese Škoda 100L?. Pues adosando a su parte posterior una especie de carretilla de dos ruedas que albergaba una caldera de vapor. El agua era calentada por unas resistencias eléctricas. Cuando se transformaba en vapor y alcanzaba una gran presión, se liberaba por la tobera que impulsaba al vehículo. Esta especie de carretilla-cohete se desconectaba del coche antes del impacto.
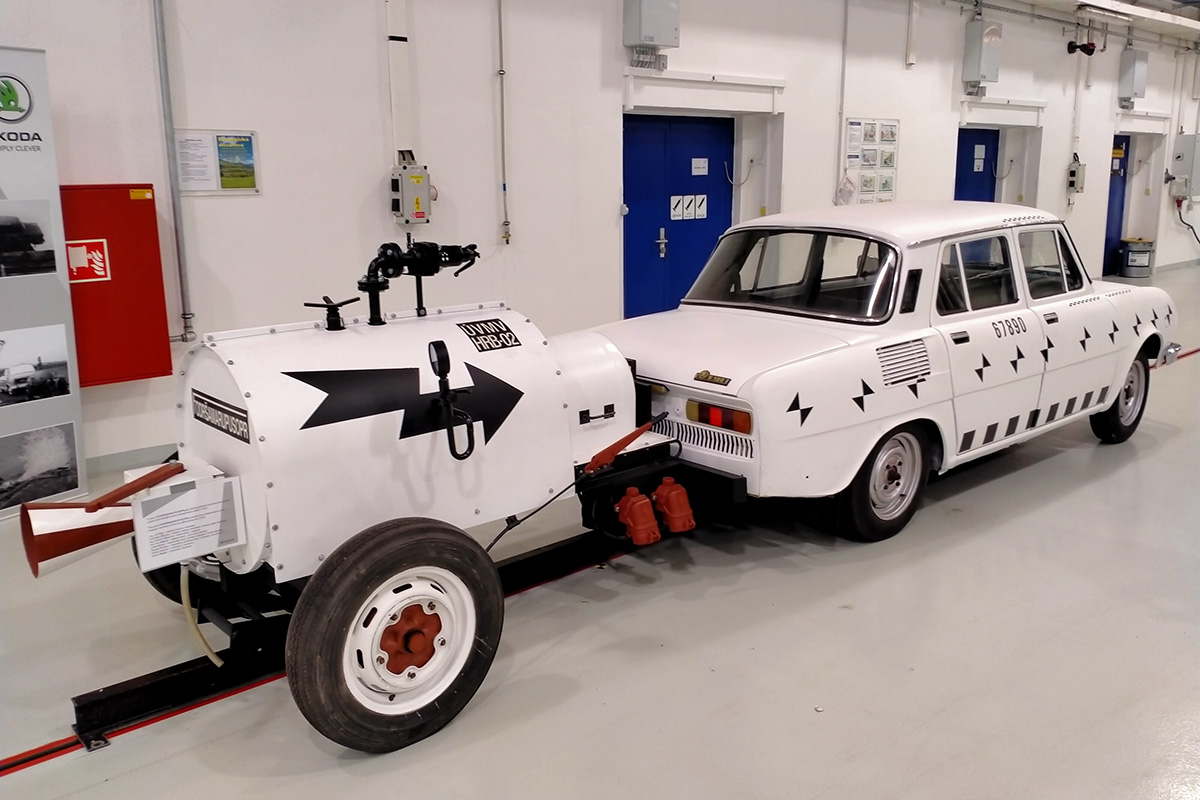
Simulación por ordenador
Hoy en día la informática toma un papel fundamental. Con los ordenadores se puede simular con un alto grado de precisión el comportamiento de una estructura frente a un impacto. Estas simulaciones permiten aislar el comportamiento de una estructura en particular ante un choque, por ejemplo, un capó. Y si no cumple las expectativas, se puede mejorar también con programas informáticos antes de poner la pieza en producción. De hecho, la mayor parte de las pruebas que hoy en día se llevan a cabo son de esta naturaleza. Škoda puede realizar unas 24 000 simulaciones por ordenador durante el proceso de desarrollo de un vehículo. Unas 1.000 preceden a la primera prueba de choque real, mientras durante la elaboración de un vehículo, se llevan a cabo unas diez pruebas de choque reales.
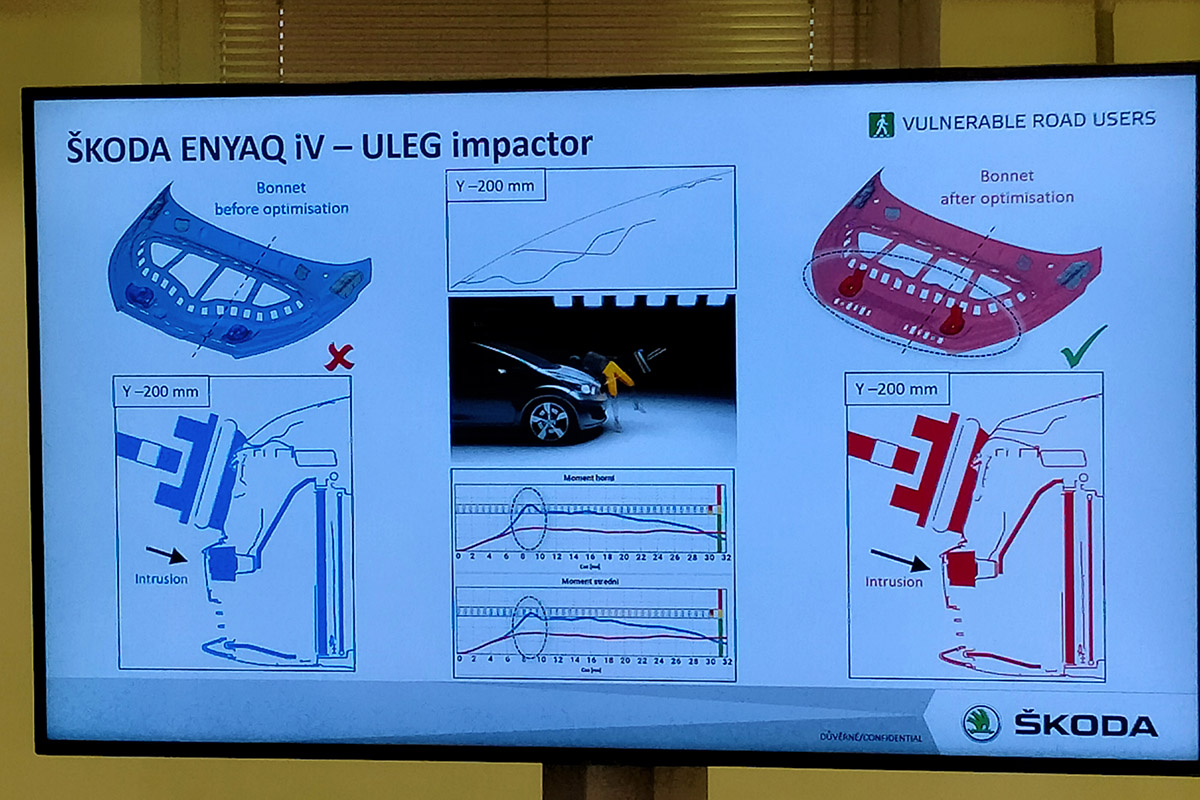
Aunque la simulación es de importancia vital a día de hoy, a medida que se avanza con el proyecto, es imprescindible hacer pruebas más o menos reales. Y aquí, como hace 50 años con el cohete impulsor, también hay que tirar de ingenio.
Simulación de partes humanas
En la prueba de atropello de peatones, se utiliza una pieza que está compuesta por dos partes rígidas con una resistencia parecida al hueso humano (fémur y tibia), unidas por una más débil que simula una rodilla y sus ligamentos. La elongación de estos ligamentos se mide mediante unos potenciómetros de cable y, anteriormente, mediante una especie de pletinas que se doblaban más o menos en función de la fuerza del impacto.
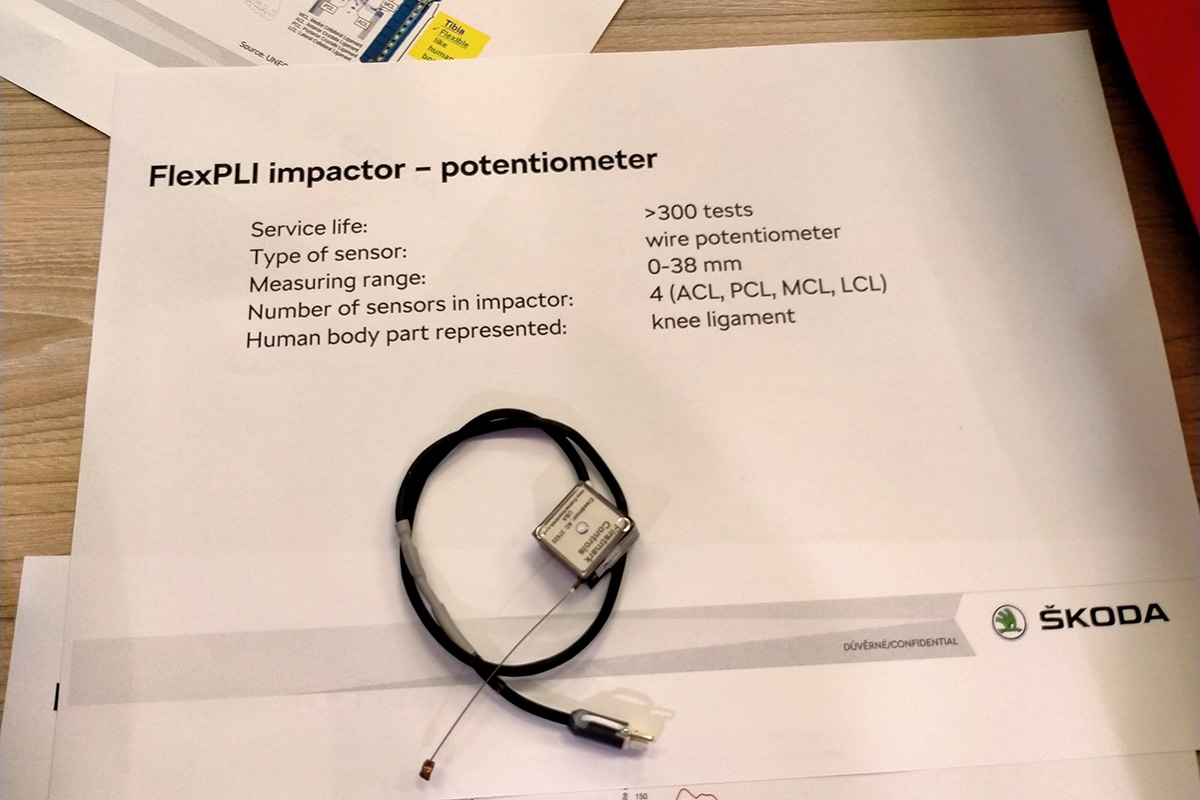
Para simular cabezas, hay una especie de esferas (de distintos tamaños y pesos; adultos y niños) con acelerómetros que determinan la fuerza del impacto sobre el capó o la luna. Para verificar el funcionamiento de las cámaras, radares y sensores ultrasónicos que sirven para evitar accidentes por alcance y atropellos, también hay coches inflables y maniquís. Para comprobar el aislamiento y estanqueidad de las baterías y los componentes de alta tensión de los coches eléctricos, hay una especie de cuba donde se sumergen los vehículos.
Que Škoda haga pruebas de seguridad no es ninguna noticia. Es algo que hacen todos los fabricantes de automóviles que venden sus coches en los mismos mercados, pues se han de amoldar a unas homologaciones. Eso no quiere decir que todos los fabricantes tengan un lugar de ensayo similar al de Škoda, ni que tengan que realizar las mismas pruebas. Por ejemplo, es posible que si un fabricante no desea ser calificado por Euro NCAP, quizá no tenga que hacer el mismo número de pruebas —ni del mismo tipo— que una que sí. Sin embargo, no por ello deja de llamar la atención la cantidad de recursos que una marca destina a estas cosas.
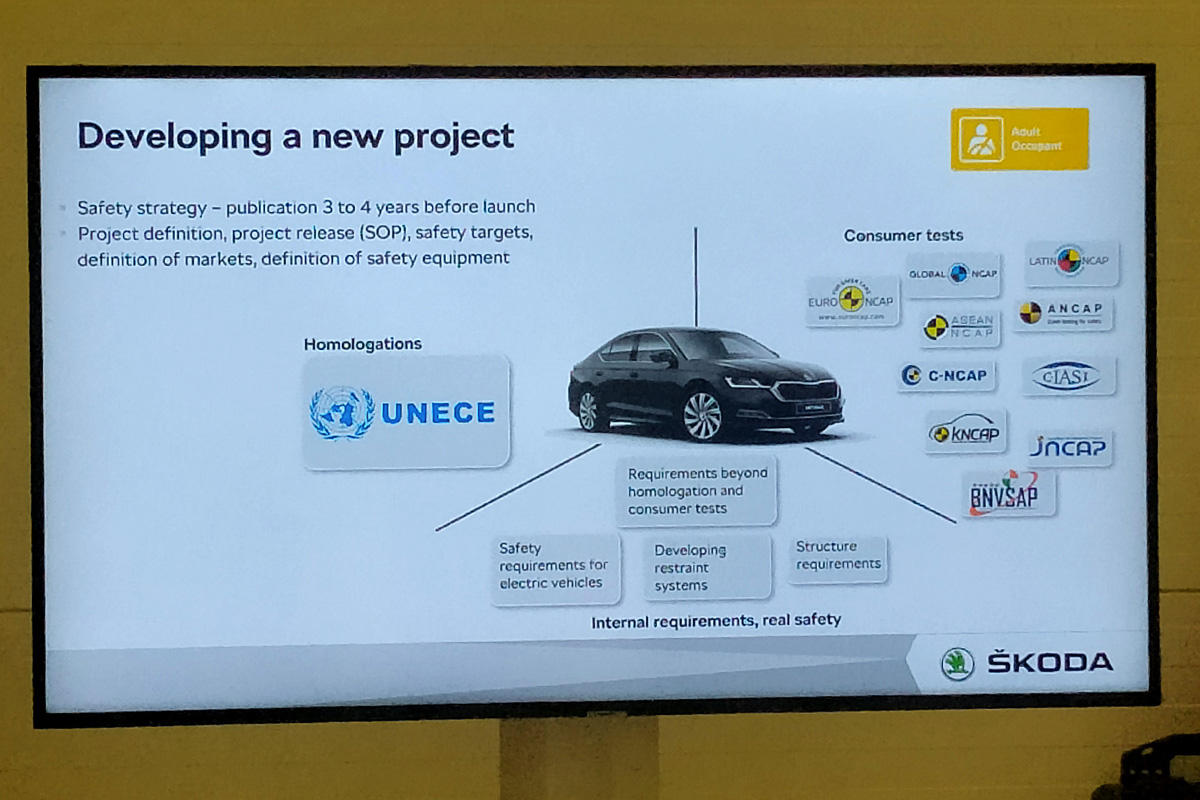
Maniquís a más de medio millón de euros
Y no sólo porque un maniquí con más de 100 canales de medición para detectar la severidad de un impacto cuesta más de medio millón de euros. Eso seguramente sea una partida pequeña dentro del gasto general de las pruebas de seguridad y una parte ridícula en los gastos de desarrollo de un coche nuevo. Cuando un fabricante se enfrenta a un nuevo desarrollo de vehículo, se debe ajustar a distintos marcos regulatorios como el que establece la UNECE, los propios requisitos internos del fabricante y, también a las pruebas externas no obligatorias de la distintas regiones (aquí en Europa tenemos la Euro NCAP, pero también hay otros organismos equivalentes fuera, como KN CAP, ANCAP, ASEAN CAP, C-CAP, LATIN CAP, GLOBAL CAP, JN CAP, CIASI o BNVSAP). Todo ello sirve para hacerse una idea general de la complejidad de este mundillo y de las grandes variaciones en el producto final que hay dependiendo de la región o país de destino.
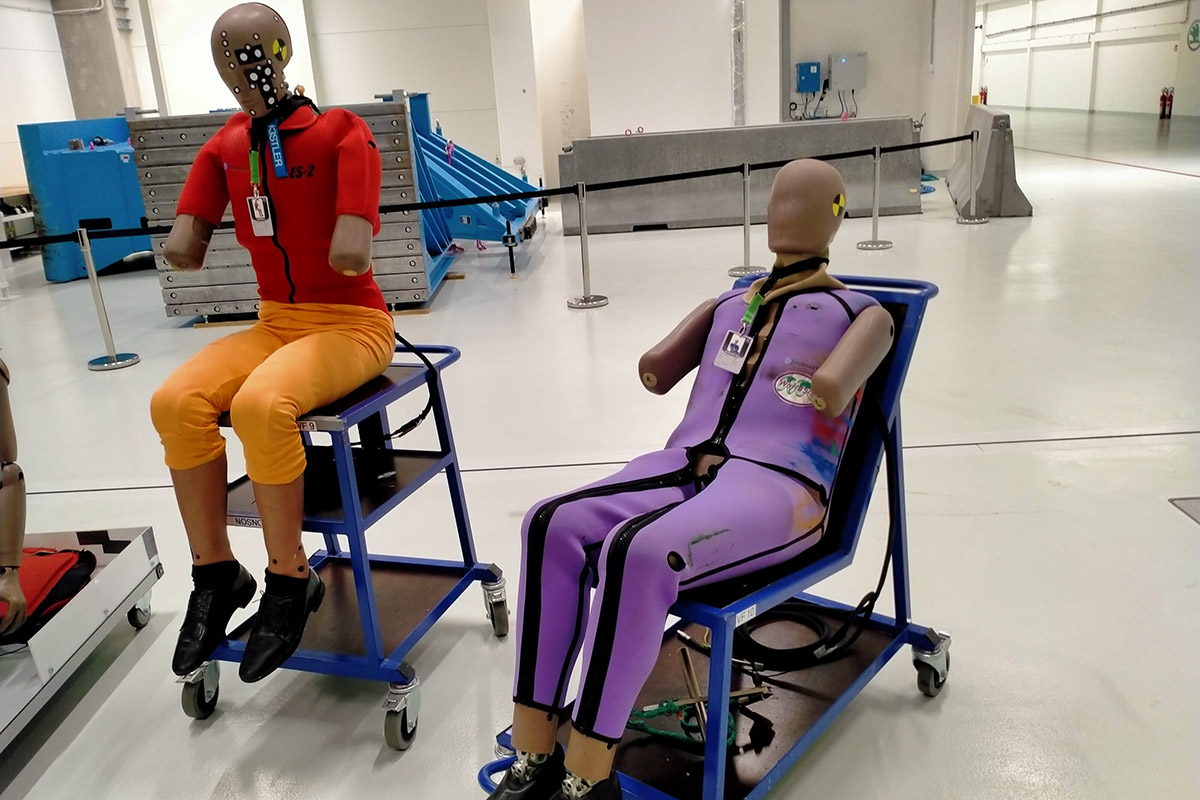
Excelente recurso; Lo estoy compartiendo con amigos para futuras investigaciones. Ha sido bastante generoso con su perspicacia; Lo aprecio.